CUSTOM PRODUCT CAPABILITIES
Rubber Molding
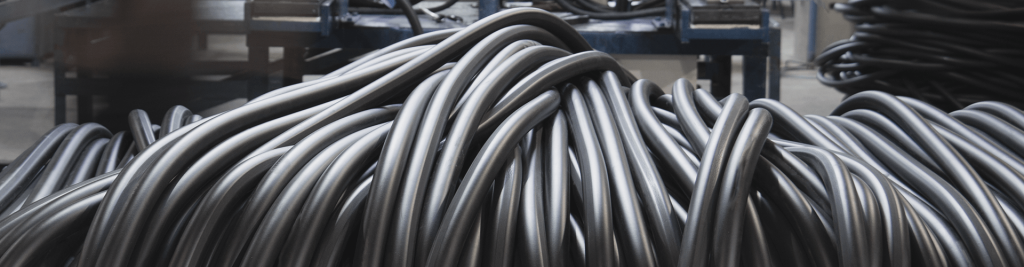
Since our founding, we have created over 600 formulations of rubber compounds used in a broad range of industrial applications.
Our rubber molding products range from a Nitrile (NBR) to a Perfluoroelastomer (FFKM).
Our chemists and lab technicians test the performance characteristics of each rubber, establishing benchmarks for tensile, elongation, tear strength, compression set, specific gravity, peel strength, and much more.
Applications
Some applications require high-precision solutions. When existing production parts aren’t up to the job, Utex can design custom molded rubber products that meet or exceed your needs.
We collaborate closely with our customers to interpret their ideas into a broad range of cost-effective rubber molding solutions, from simple ID/OD rings to complex rubber parts with sophisticated geometric profiles.
Over the years, our custom rubber molding process has produced more than 5,000 unique parts that are now used in industries including oil and gas, petrochemical, medical, pulp, and paper facilities.
Rubber Molding Categories
Compression Molding
One of our most common methods of molding rubber, Compression Molding requires some early steps of making preforms. A preform is placed into the mold and then compressed in the mold under specific temperature and pressure for the size and material of the finished part. Flashing, excess material, may occur and needs to be trimmed at a later stage.
Injection Molding
During Injection Molding, heated rubber travels through an auger, where it is softened and then forced through a nozzle into the mold cavity. While in the cavity it will take its shape as it cools before being removed. This is the most efficient process of the four methods because it allows for quick production of high quantity parts.
Transfer Molding
Transfer Molding is similar to compression molding yet the mold is more complex, requiring a transfer pot that has a small passage to the actual mold cavity. Rubber is placed in the transfer pot and heated prior to being forced into the mold cavity to form the molded part.
Extruded Rubber
When extruding rubber, strips of raw rubber are fed through one side of a barrel where they will be rotated through along the screw all while heating up along the length of the barrel. On the opposite side, there is a metal die that the rubber is forced through, taking take the shape (or profile) of the die. After the rubber comes through the die, we run it through a chilled water bath to help maintain the final profile.
5 Steps for Custom Rubber Molding
1. Concept
Utex has partnered with hundreds of customers over our 80-year history to conceptualize and model new and existing technology. Combining the knowledge of our engineering, materials, and manufacturing teams, Utex can create a solution for whatever problem you are facing.
2. Formulation
Utex has over 600 proprietary compounds to choose from for your application. Our in-house formulating, mixing, and molding capabilities reduce the number of companies required for your project, and guarantee that your material is properly managed.
3. Prototyping
Want to prove your concept before producing on a mass scale? No problem! Utex offers a rapid prototype division to produce prototype parts quickly and efficiently for fast testing and evaluation.
4. Construction
Utex offers all manners of part construction, including cast-molded and foamed urethane compression, injection and transfer molding, machining of rubber, thermoplastics, and metal, bonding rubber and/or thermoplastics to metal or other substrates, and spring installation and fabrication.
5. Production
No matter what volume you need, Utex has an efficient method to produce the quantity you need. Through our in-house mold design and machining teams, we can ensure your product is made of the highest quality to meet even the most stringent performance requirements.
That Rubber Molding question you have? We've got the answer to it.